The author is a retired dairy nutrition consultant who worked with farms across the country.

Dairy farms of all sizes are challenged with properly disposing and managing the manure produced by their herds. The larger the dairy, the greater the challenge becomes in containing and managing effluent, solids, volatiles such as ammonia, and, more recently, odor. While manure is universally accepted as an indispensable source of plant nutrients and soil amendments, many dairies have limited access to adequate land or the ability to dispose of their manure in a timely or an environmentally responsible way.
It’s an issue that can no longer be swept under the rug. For many years, the mainstream press has had a field day demonizing animal agriculture in general and dairy farming in particular as major polluters of nitrogen and phosphorus as well as volatile gases such as methane and ammonia polluting the atmosphere and emitting odors.
For all the challenges associated with manure, there’s a positive side to this organic material as a source of renewable energy that goes well beyond its traditional use as a fertilizer. Emerging over the last decade is a growing industry focused on collecting and marketing the biomethane produced by the anaerobic fermentation of manure.
One farm’s story

The cows are milked 3x in two parlors — a double-50 parallel and an 80-cow rotary. Milk production ranges from 70 to 90-plus pounds of milk per cow per day and is profoundly affected by Georgia’s summertime heat and humidity.
In 2016, Graft began the process of building an anaerobic digestion system that met his requirements for properly managing manure and reducing odors. He noted that there are many companies that have entered the manure digestion and methane production business. However, not all are fully knowledgeable of how to construct large anaerobic digesters or offer round-the-clock management of those systems.
Graft chose to work with Vanguard Renewables because of their successful track record of installing and operating both manure only and co-digestion systems on dairies with a large range of herd sizes. They also supply the capital necessary to install the systems, eliminating the need for dairy farms to come up with the finances to fund such a project, which would be substantial.
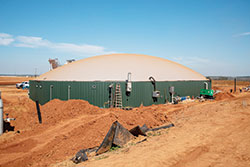
On freestall dairies like Graft’s, manure effluent, primarily coming from flushing freestalls, is quickly transported into sealed lagoons where the gases cannot escape. It’s in the sealed lagoons where the marketable by-product, methane, is produced, captured, processed on-site, and piped directly into the local natural gas utility’s pipeline.
According to Kevin Chase, co-founder and chief development officer at Vanguard Renewables, any dairy farm, large or small, has the ability to produce methane from the manure produced. On smaller dairies, the company adds food waste to the manure in a process known as co-digestion. A manure-only digester is an expensive undertaking to build, manage, and maintain. Most importantly, there must be an adequate amount of manure available to justify the investment.
Chase says that for his company to consider a manure-only system financially viable, there needs to be a minimum of 5,000 to 10,000 wet-cow (milk-cow) equivalents available. He has systems in operation on both single sites as well as groups of dairy farms that are in close geographic proximity to share the infrastructure. The company looks specifically to partner with dairy farms that are interested in proactive approaches to mitigating environmental pollution and positioning their dairy farms in a positive light in their communities.
More income opportunities
With the 7,000 milking cows along with the heifers and dry cows on the property, Leatherbrook Holsteins met the requirement to be a stand-alone methane producer that uses only the manure produced on the farm without having to add additional organic material to maximize methane production. The dairy derives two income streams through the partnership — a lease payment for the land being used and a payment for the manure used in the digestion process.
Graft explained that the digestion system reduces the massive amount of manure solids to about one-fourth the volume of material while still containing all the nutrients. The digestate material remaining after the digestion process is pumped out of the digesters and temporarily stored in a small lagoon. From there it’s pumped out to the cropland via a drag-hose system, which includes about 6 miles of underground pipeline.
The drag-hose system allows Graft to move a lot of fertilizer rapidly in a liquefied form, which enables it to be injected into the ground. This reduces the volatilization loss of spreading fertilizer on the ground surface and enables more nitrogen to be delivered for plant uptake. In addition to the more efficient delivery of nutrients, this system completely eliminates the need for daily hauling and spreading, or the need to stockpile solids, which creates the potential for odors, runoff, and ground water contamination.
The system at Leatherbrook Holsteins is designed to produce 200,000 million British thermal units (MMBtu) per year, which provides the energy-equivalent of over 58,000,000 kwh. According to the U.S. Department of Energy, the average home in the U.S. uses about 900 kwh of electricity per month or about 10,800 kwh/year. Therefore, the energy provided by the collected methane at Leatherbrook Holsteins can provide enough energy to power over 5,000 homes for a year.
The raw biogas that comes directly out of the digester is not pure methane and must be purified before it can be delivered to a local utility. The purification process is completed at the site and includes the removal of water vapor, carbon dioxide, sulfides, and nitrogen compounds, which are all by-products of the anaerobic process. The purified methane is then piped about 2 miles to a location where it joins a local utility’s natural gas line.
Partners for the future
As U.S. dairy farms grow in size, they become bigger targets for a critical public and more vulnerable to environmental pollution and legal actions. While dairy farms are certainly not the primary producer of methane escaping into the atmosphere, they do need to take a proactive approach in helping mitigate unnecessary levels of this potent greenhouse gas that’s contributing to the changes in weather patterns around the world.
When opportunities exist, partnering with an environmental management company that provides technology, management, and capital is a brilliant way for dairy farms to manage manure and odors, capture a potent greenhouse gas, and cash in on its value as a renewable source of energy. At the same time, dairy farms can be part of the solution, not part of the problem, in protecting our fragile environment.
This article appeared in the February 2023 issue of Journal of Nutrient Management on pages 16-18. Not a subscriber? Click to get the print magazine.